The Role of Industrial Blenders in Modern Manufacturing
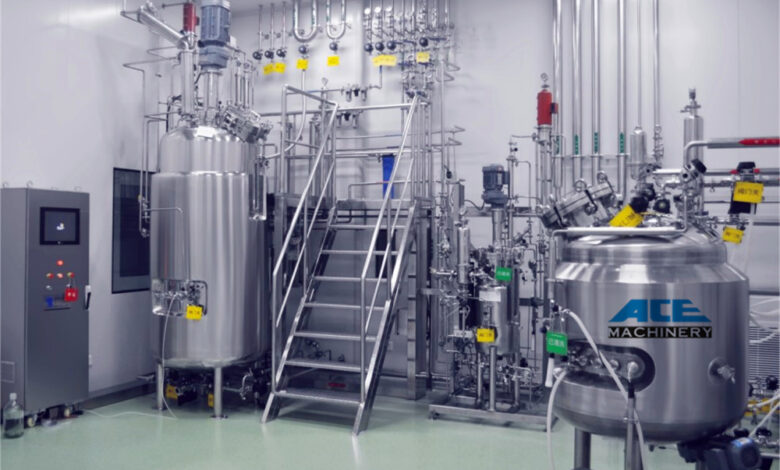
Key Takeaways:
- Industrial blenders enhance efficiency and product consistency in various manufacturing sectors.
- Knowledge of the different types of blenders and their specific uses can significantly improve manufacturing processes.
- Continual technological innovations are revolutionizing blender operations, adding value across industries.
Introduction to Industrial Blenders
In the hustle and bustle of modern manufacturing, industrial blenders operate quietly yet efficiently, performing a critical task—mixing. These machines are the backbone of numerous manufacturing processes, ensuring materials are blended to the right consistency and texture. Their importance extends across various industries, where they play a pivotal role in determining the quality of the final product.
Blenders cut across boundaries and are used for mixing spices in the culinary world or amalgamating chemicals in the pharmaceutical sector. In many industrial settings, an industrial mixer is essential for handling large-scale production demands, ensuring that ingredients are uniformly blended to meet stringent quality requirements. Understanding their integral role and functions can unlock new levels of efficiency, offering insights into optimizing production lines for enhanced quality and performance. This knowledge can drive changes that ensure product consistency, ultimately boosting customer satisfaction and compliance with industry standards.
Types of Industrial Blenders
Ribbon Blenders
Ribbon blenders are the workhorses of the mixing world, designed for versatility and precision. These blenders are adept at handling various materials, featuring helical ribbons that rotate within a U-shaped trough. This makes them indispensable for industries that carefully combine solid and liquid components. Their ability to uniformly mix materials of different textures and densities without excessive heat buildup or product degradation is unmatched.
Paddle Blenders
Paddle blenders excel in their gentle yet effective mixing action, making them ideal for applications necessitating careful handling. The design incorporates several paddles attached to a rotating shaft and carefully tumbles the materials, ensuring an even mix. This method is particularly advantageous for formulations susceptible to damage from too vigorous blending, such as friable materials or high-moisture-content mixtures. Their application spans various industries, from food to pharmaceuticals, each with unique blending needs.
V-Blenders
The striking V-shape of these blenders serves a purpose suited to delicate operations, where gentle rotation is crucial. V-blenders are renowned for their efficiency in mixing without the risk of particle degradation, making them ideal for blending fine powders that require precision. Their non-intensive blending mechanism is perfect for operations where maintaining the integrity of the materials is paramount, solidifying their place in sectors like pharmaceuticals, where precision is key.
Applications in Various Industries
- Food and Beverage: Blenders ensure consistency and flavor uniformity in products, from sauces to spice blends, which is critical for maintaining brand identity and consumer satisfaction.
- Pharmaceutical: In this industry, precision mixing can mean the difference between life-saving medication and a product that falls short. Blenders ensure that active ingredients and excipients are mixed to exact specifications, ensuring efficacy and safety.
- Chemical: Industrial blenders handle the rigorous requirements of chemical production, ensuring homogeneous mixtures vital for research and application processes.
- Cosmetic: The cosmetic industry relies on blenders to mix lotions, creams, and gels to a consistent texture and quality, which is important for product performance and user satisfaction.
Technological Advancements
Technological advancements in the blending industry pave the way for greater efficiency and innovation. Modern blenders now come equipped with intelligent control systems and automation, allowing for precise settings and real-time monitoring. These improvements significantly reduce the chance of human error and enhance the overall consistency of the product. The integration of smart technology and automation not only optimizes the blending process but also aligns with safety standards and regulatory requirements.
Efficiency and Consistency in Production
One of the primary advantages of using industrial blenders is the efficiency they bring to the production line. By standardizing processes and reducing variations, these machines help maintain the consistency of the end product. With increasing consumer demand for quality, having a reliable method of ensuring every batch meets stringent quality standards is essential. Thus, industrial blenders are indispensable, particularly in high-volume industries where time and quality cannot be compromised.
Key Considerations When Choosing Blenders
Choosing the right industrial blender involves evaluating several factors to match specific production needs. Consider the blender’s capacity in relation to the scale of your operations. Additionally, material compatibility should be assessed, as certain blenders are better suited for particular substances, whether they be corrosive chemicals or delicate powders. Energy efficiency can also be critical in long-term cost savings, especially in large operations. It’s also prudent to examine maintenance requirements and the durability of the equipment, as these factors can affect operational uptime and product longevity.