Hidden Impacts Control Integrators Have on Long‑Term System Reliability
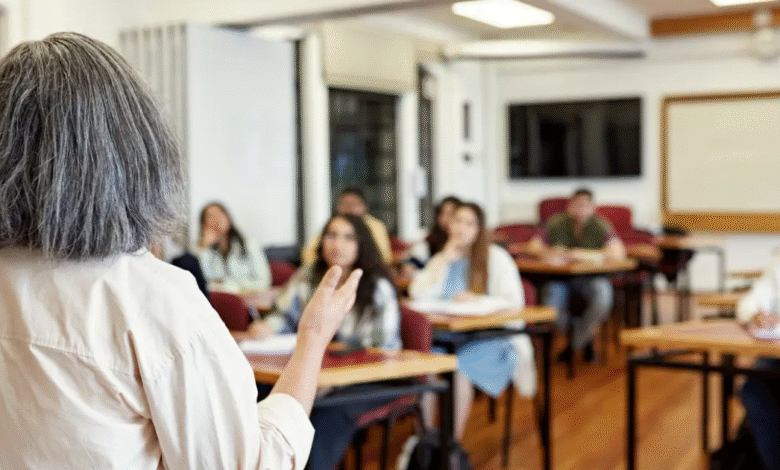
It’s easy to spot a good control system by how well it runs today. What’s harder to see—yet far more important—is how reliably it performs years down the line. Behind that silent efficiency, control integrators play a much bigger role than you might expect. Their design choices, protocols, and maintenance foresight shape how a system holds up over time.
Enhanced Fault Tolerance Through Redundant System Design
Redundancy isn’t just a safety net—it’s a forward-thinking strategy. Skilled control integrators design systems with backup components and mirrored processes that quietly take over when the main ones fail. Whether it’s redundant servers, failover PLCs, or dual communication paths, these systems continue running smoothly even when something breaks. Without this built-in insurance, a single failure could mean hours of downtime or worse, damaged equipment.
That kind of resilience doesn’t happen by accident. It’s the result of intentional planning during the control system integration process. Engineers with experience in SCADA integration know how to balance cost and coverage to protect critical operations. Over the years, this level of redundancy keeps systems online longer, even in unpredictable environments where failures are inevitable.
Subtle Influence of Integrator’s Protocol Standardization on Longevity
Not all protocols play well together. A major hidden benefit of control integrators is their ability to standardize communication across complex systems. By aligning devices and platforms under streamlined, well-supported industrial protocols, they reduce communication errors and long-term compatibility issues. This doesn’t just make things run smoother—it actually extends the life of the system itself.
It’s often overlooked, but mismatched protocols or haphazard configurations can shorten component life and make future upgrades expensive or even impossible. Good SCADA integrators enforce consistency during setup, using proven communication standards that make maintenance easier and reduce the risk of system-wide glitches years down the road.
Increased Stability from Integrated Condition-Based Monitoring
A well-integrated system doesn’t just operate—it listens. Through condition-based monitoring, control system integration allows machines to report their health in real time. Sensors feed data back into control logic, helping operators spot mechanical wear, rising temperatures, or vibration trends before anything fails. This subtle feedback loop reduces surprises.
More importantly, it means that interventions can happen early, minimizing unplanned downtime and expensive emergency repairs. With continuous oversight engineered into the system from day one, stability improves year over year. Control integrators who build in monitoring functionality give companies long-term visibility and control that reactive systems can’t match.
Impact of Structured Data Logging on Predictive Maintenance Accuracy
Data logging isn’t just about records—it’s about insight. A key decision made during control system integration is how, where, and what to log. Proper structure allows data to be used for trend analysis, failure prediction, and lifecycle planning. Poor or incomplete logging, on the other hand, leaves operators blind to performance issues developing over time.
The right control integrators create tagging structures and logging strategies that capture what matters most, making predictive maintenance more than a guess. Accurate data helps technicians prevent failures before they happen. Over time, this lowers costs, increases uptime, and adds serious longevity to everything from motors to pumps to PLCs.
How Rigorous Configuration Management Safeguards System Reliability
Small changes to code or hardware settings can create unexpected ripple effects. Without configuration management, these tweaks go undocumented—and when something goes wrong, no one remembers what changed. Control integrators prevent this mess by implementing structured change tracking from day one, creating a log of every adjustment, firmware update, or patch.
This approach ensures consistency and traceability, especially when new engineers step in or upgrades happen years later. Systems with managed configuration histories are more resilient during failures and recover faster because there’s no guesswork. That level of reliability is invisible on the surface but critical to the system’s long-term health.
Long-Term Gains from Consistent Firmware Management Practices
Control systems evolve, and so does the firmware running them. Control integrators who manage firmware updates across devices ensure that critical patches are applied without breaking compatibility. This protects the system from both bugs and cyber threats that can creep in through outdated versions. Keeping everything in sync avoids failures triggered by misaligned firmware levels.
The benefits stack up slowly over time. Well-managed systems experience fewer crashes, smoother updates, and longer device lifespan. Firmware management might not sound glamorous, but it’s a quiet discipline that reinforces every layer of system reliability from control panels to sensors.
Systemic Reliability Boost Through Optimally Engineered Control Loops
The design of control loops is where science meets intuition. Poorly tuned loops lead to erratic performance, overcorrection, and unnecessary strain on mechanical parts. But expertly engineered loops, guided by skilled control integrators, deliver stable and efficient operation day after day. They prevent excess wear and allow machinery to perform smoothly even under shifting loads.
These optimizations add up. Reduced mechanical stress leads to fewer breakdowns and longer equipment life. Operators spend less time chasing problems, and maintenance becomes more predictable. Behind that polished performance is an integrator who understood the system well enough to build something that lasts—and keeps lasting.