Old but Reliable: Micah Chaban Talks FDM’s Role in Modern 3D Printing
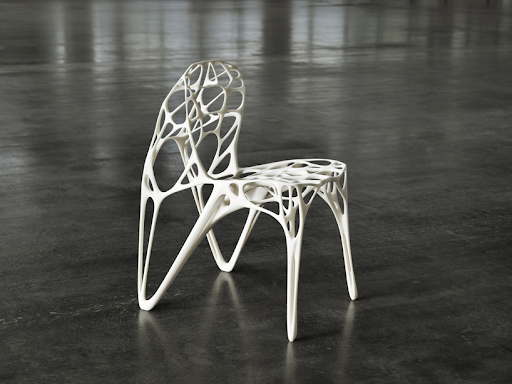
Micah Chaban is the Founder and VP of Sales at RapidMade, a digital manufacturing company known for delivering engineered solutions in 3D printing, machining, and thermoforming. With a background in product development and a keen eye for application-specific manufacturing, Micah has spent over a decade helping engineers turn digital designs into physical parts. In this interview, he shares practical insights into one of the most common but often underestimated technologies in additive manufacturing: Fused Deposition Modeling (FDM).
What makes FDM still so relevant in today’s advanced additive landscape?
FDM remains the backbone of practical 3D printing. Sure, there are flashier technologies—SLA, SLS, MJF—but FDM offers a combination of speed, affordability, and material flexibility that’s hard to match, especially for functional parts. It’s a process that’s matured from basic prototyping to serious industrial use, particularly when you’re working with durable thermoplastics or need tooling, fixtures, or short-run production.
Can you walk us through how the process actually works?
It’s surprisingly simple, which is part of its strength. You feed thermoplastic filament through a heated nozzle, and the printer deposits the material layer by layer to form your part. The key to good FDM printing is managing the thermal behavior of the material—making sure the layers bond properly and that you’re not introducing warping or internal stresses. It’s easy to start printing, but hard to master without understanding how geometry, orientation, and temperature interact.
Let’s talk about materials. What are engineers typically using, and why?
That’s one of the biggest reasons engineers stick with FDM—it supports a huge range of materials. For basic prototyping, you’ll see PLA and ABS. For more functional parts, PETG is popular for its chemical resistance and ease of printing. Nylon gives you strength and wear resistance. TPU is flexible and great for damping. Then you’ve got high-performance materials like PEI—better known as ULTEM—which we use in aerospace and medical applications where thermal or chemical resistance is non-negotiable.
What’s also exciting is the use of composites like carbon fiber-filled nylon. These materials give you the strength and stiffness of machined parts without the time and cost.
What are the most important design considerations when working with FDM?
Layer orientation and geometry are critical. The Z-axis is your weak point because of the way layers bond—so you need to orient your part with mechanical loads in mind. You also need to avoid thin unsupported features, sharp overhangs, and assume that holes may need to be reamed post-print. We help customers build around those constraints—sometimes literally.
FDM isn’t perfect, but when you design with its strengths in mind, it’s incredibly effective. You can consolidate assemblies, create complex internal channels, or rapidly iterate without the friction of traditional tooling.
How much post-processing is typically involved?
That depends on the part. For purely functional jigs or tools, maybe nothing more than support removal. For customer-facing parts or things that need to mate precisely, we’ll do some sanding, vapor smoothing for ABS, or light machining to bring key features into tolerance.
We treat post-processing as part of the design process. If you know a feature’s going to be machined after printing, you build in the tolerance from the beginning.
What industries or applications are getting the most from FDM?
Manufacturing and industrial tooling are still the sweet spots. Companies use FDM for jigs, fixtures, custom guides—anything that helps keep production lines moving without long lead times or high costs. Aerospace uses it for lightweight ducts and brackets. Automotive teams are printing prototypes, testing fits, or creating check gauges.
In medical and healthcare, we’re printing surgical models, device enclosures, and patient-specific tools using sterilizable materials. And in consumer products, it’s great for quick iterations or even short-run production.
FDM isn’t perfect. Where do you see its limitations?
The main ones are resolution, surface quality, and mechanical anisotropy. You’re never going to get the fine detail or ultra-smooth finish of SLA or MJF with FDM. And strength is directional—parts are weaker along the layer lines. That’s why orientation and design are so important.
You also need to be realistic about tolerances. FDM is reliable when you design around its parameters, but it’s not a replacement for CNC in high-precision applications. It complements machining; it doesn’t replace it.
How does FDM compare to other additive methods, in your view?
Each process has its lane. SLA is great for small, detailed, cosmetic parts. SLS and MJF offer isotropic strength and smoother finishes but with higher cost and longer prep times. FDM is the most flexible, fastest to deploy, and easiest to scale on short notice. It also has the broadest material library, which is key for engineers looking to prototype in the same material they’ll use in production.
So it’s not about FDM vs. the rest—it’s about knowing when to use each tool.
Final thoughts for engineers considering FDM?
Use it thoughtfully. Don’t just print because you can—print because it solves a problem better than other options. Whether it’s saving time, cost, or reducing risk, FDM is incredibly capable when applied correctly. And lean on people who’ve done it before. There’s a lot of nuance that doesn’t show up in a slicer preview or a spec sheet.
Looking to take full advantage of FDM in your engineering workflow?
Reach out to RapidMade for design guidance, material selection, and production-grade 3D printing solutions.
Visit rapidmade.com or email info@rapidmade.com to get started with the best 3D printing services in the USA.